¿Qué son los suelos y pisos de resina epoxi y para qué se utilizan?
Un piso de resina epoxi es la solución para proteger su piso al tiempo que proporciona una nota decorativa moderna y contemporánea. Después de haberse establecido como un campo de referencia industrial por su robustez y su velocidad de aplicación, el piso de resina está actualmente en pleno desarrollo en el interior. Las ventajas que ofrece este innovador producto (resina epoxi) son múltiples: elegante, económico, resistente al desgaste , sin costuras y fácil de mantener.
El suelo de resina epoxi es especialmente adecuado para áreas sujetas a tráfico peatonal, montacargas y tráfico de vehículos, como fábricas, garajes, salas de exposiciones, salas de trabajo y aplicaciones industriales, pero también para la protección de su piso de garaje, estacionamiento, área de almacenamiento, bodega, lavadero o taller… Evita la formación de polvo al detener el desgaste natural del hormigón. Más resistente al impacto y la abrasión que el hormigón, su resistencia química superior puede proteger eficazmente su suelo contra la mayoría de los contaminantes (aceite, ácido, agua salada…). Un revestimiento de suelo de resina diseñado para áreas donde se necesita un piso antideslizante, como áreas de producción de alimentos, lecherías y mataderos.
Colores brillantes o pasteles. El aspecto estético de un piso de resina epoxi no se queda atrás ya que las posibilidades de coloración son múltiples y se pueden agregar elementos decorativos como brillo.
¿Por qué un suelo de resina?
Rápido, fuerte y estético, tres grandes activos de la resina. La resina epoxi permite pisos sin juntas y continuos, que cumplen con los estándares técnicos y todas las demandas del mundo industrial:
- 3 veces más fuerte que el hormigón.
- Mejor rendimiento que el hormigón frente al desgaste y la abrasión.
- Estabilidad a altas temperaturas (choque térmico).
- Facilidad de mantenimiento diario (especialmente polvo).
- Resistencia al ataque químico (ácidos).
- Piso antiestático, piso antideslizante, conductor, piso acústicamente aislante.
- Cumplimiento de estándares para suelos agrícolas.
- La resina también es un producto inodoro y no contiene solventes.
Los pavimentos de hormigón están expuestos a constantes agresiones mecánicas y químicas. Todo nuestros revestimientos de pavimentación en continuo proporcionan alta protección, buen acabado y gran facilidad de mantenimiento y limpieza, aspectos vitales para garantizar el desempeño y la durabilidad.
Propiedades de los pavimentos epoxi
- Excelente adherencia al hormigón, el mortero y la piedra.
- Buena resistencia mecánica a la abrasión y el impacto.
- Buena resistencia química.
- Impermeable al agua.
- Acabado decorativo, gran variedad de colores con acabado brillante o satinado. Liso o rugoso.
En el Documento Básico SU «Seguridad De Utilización» se define que los pavimentos destinados a este uso deben disponer de una resistencia al deslizamiento de clase 3, cuya resbaladicidad debe de ser de RD>45.
Así mismo, en el Documento Básico SI “Seguridad en Caso de Incendio”, se define actualmente, tras las modificaciones introducidas recientemente, que la clase de reacción al juego de los materiales en acabados de los pavimentos de aparcamientos debe ser de BFL-s1.
Además, se requiere que estos acabados posean suficientes resistencias para resistir al tipo de acciones mecánicas de abrasión y desgaste que producen los neumáticos, así como las agresiones químicas producidas por líquidos corrosivos e hidrocarburos que se vierten accidentalmente en este tipo de instalaciones.
Los puntos fuertes de los pavimentos basados en resinas epoxi
Los pavimentos especiales compuesto de resina epoxi se caracterizan por una alta resistencia a factores mecánicos, químicos y condiciones medioambientales desfavorables. Son más higiénicos que los suelos tradicionales, porque la ausencia de juntas facilita la limpieza y son más atractivos desde un punto de vista estético, ya que es posible utilizar una amplia gama de colores.
Las aplicaciones son muy diversas y pueden ser utilizados en la industria química, siderometalúrgica, agroalimentaria, mataderos, hospitales, quirófanos, recintos deportivos, centros comerciales, aeropuertos, hangares de aviones y, en general, en todas aquellas superficies sometidas a un desgaste intenso, pero no por esto no pueden ser utilizados en su propio garaje particular.
La aplicación de los pavimentos especiales puede realizarse de acuerdo con alguno de los siguientes sistemas:
- Pinturas.
- Autonivelantes.
- Multicapa.
- Mortero seco.
¿Por qué las resinas epoxi?
Las tres mayores fortalezas de la resina son las siguientes:
- Rápidas.
- Fuertes.
- Estéticas.
Las resinas se pueden ejecutar sin fisuras, que cumplan las normas técnicas y las exigencias del mundo industrial.
- Tres veces más resistentes que el hormigón.
- Más resistentes al agua.
- Mejor rendimiento que el hormigón contra el desgaste y la abrasión.
- Estabilidad a altas temperaturas (choque térmico).
- Facilidad de mantenimiento sobre una base diaria (incluido el polvo).
- Resistencia a los ataques químicos (ácidos).
- Antiestático, antideslizante, antiestática y aislante del nivel de ruido.
- El cumplimiento de normas alimentarias (Directiva 93/43 CEE del 14/06/93).
Utilidades de las resinas epoxi
Algunas imágenes de suelos con resinas Epoxi
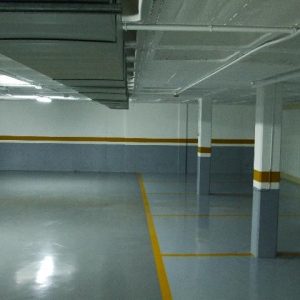
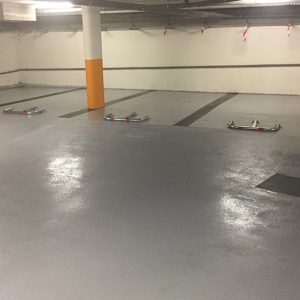
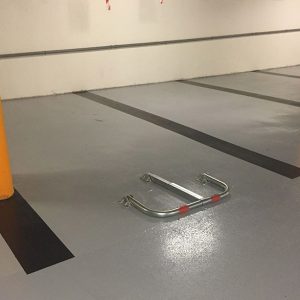
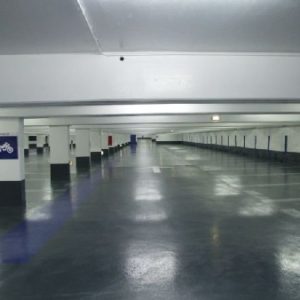
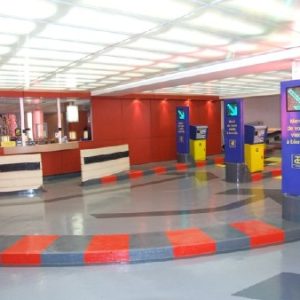
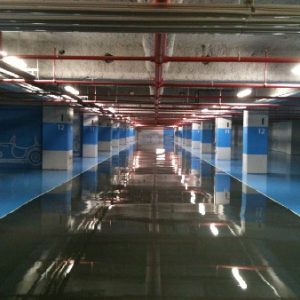
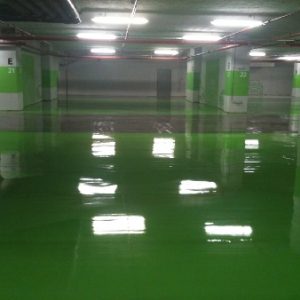
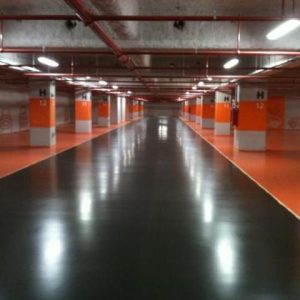
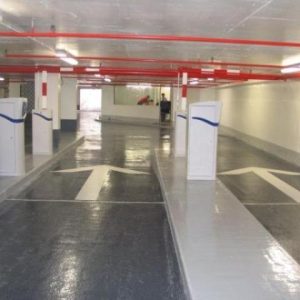
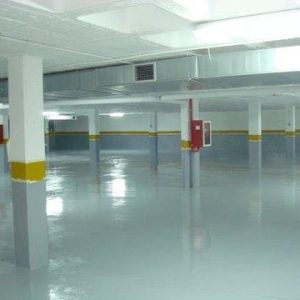
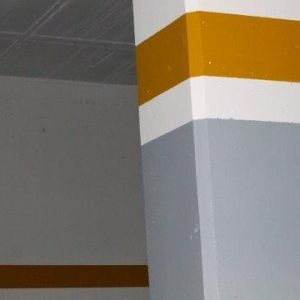
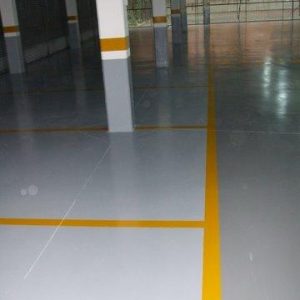
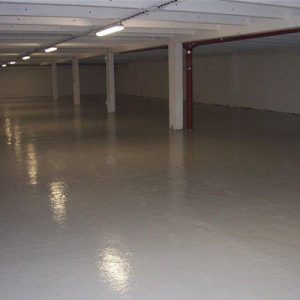
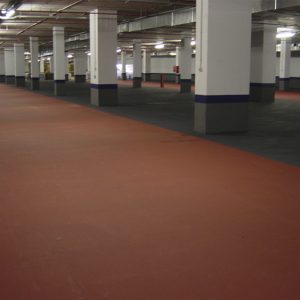
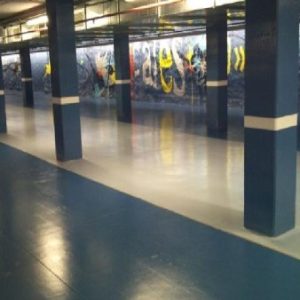
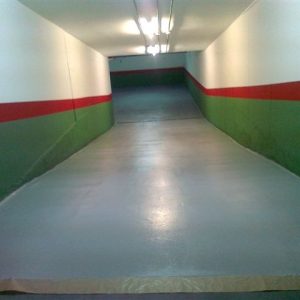
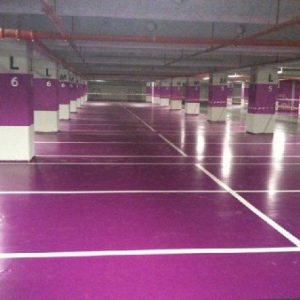
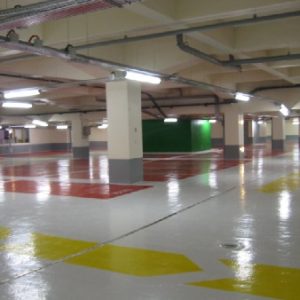
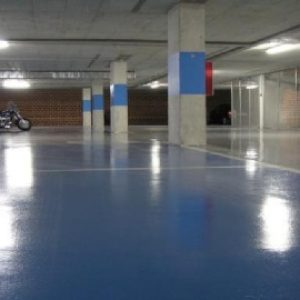
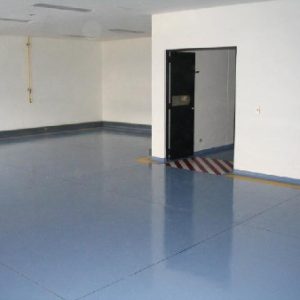
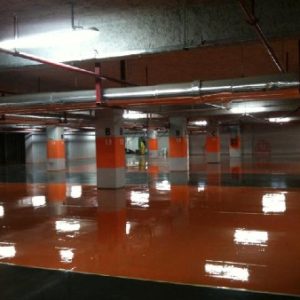
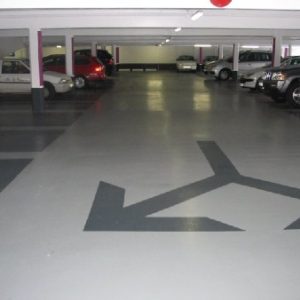
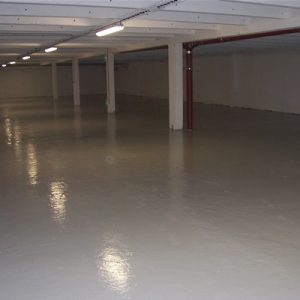
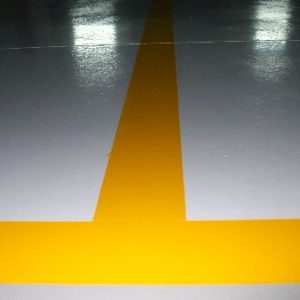
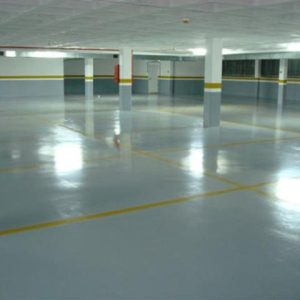
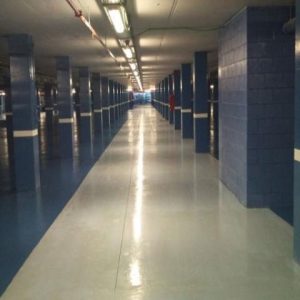
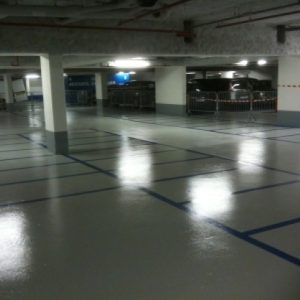
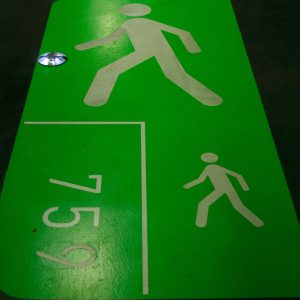
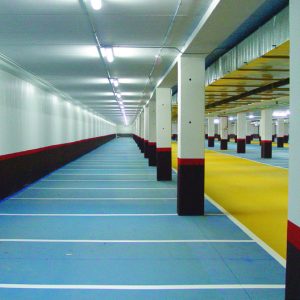
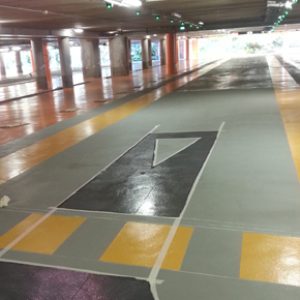
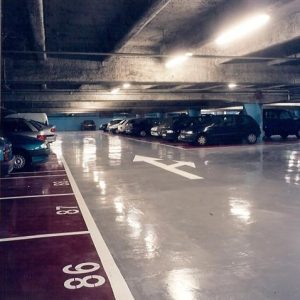
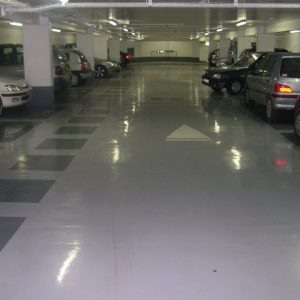
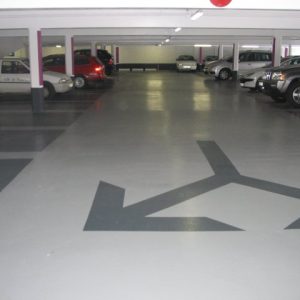
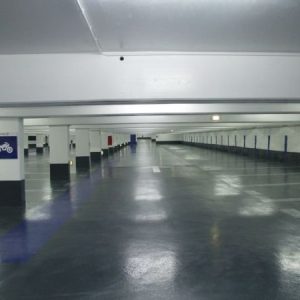
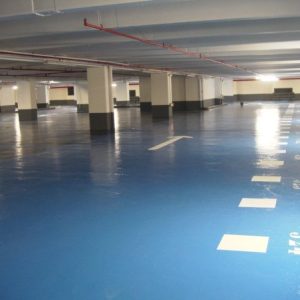
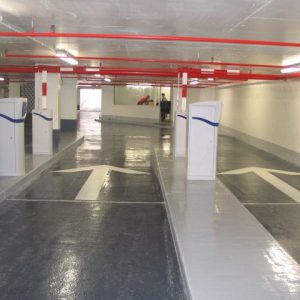
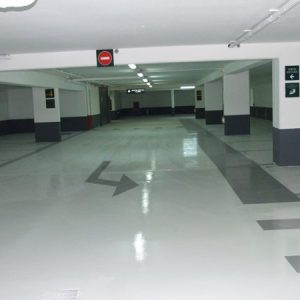
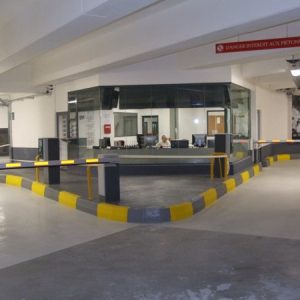
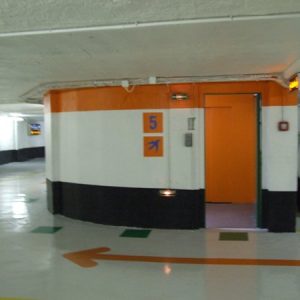
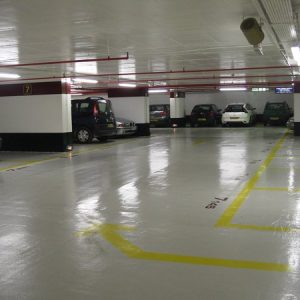
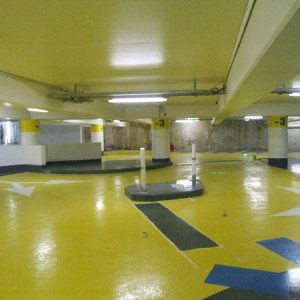
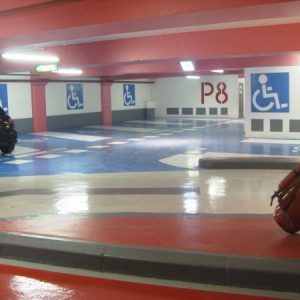
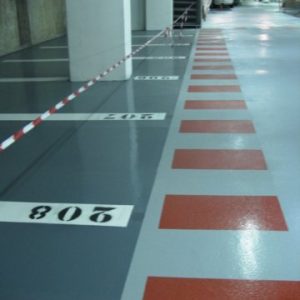
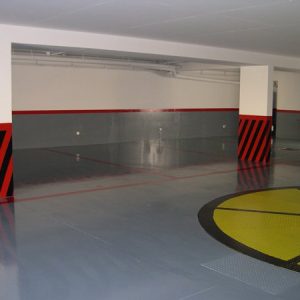
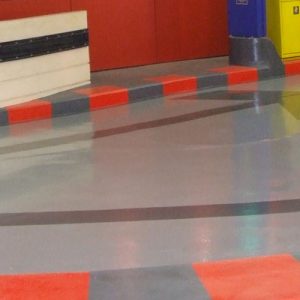
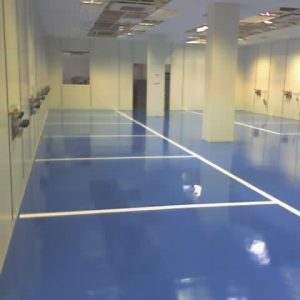
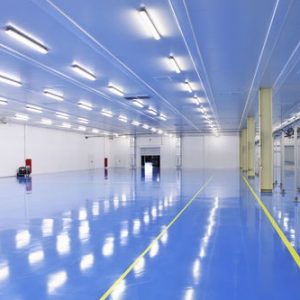
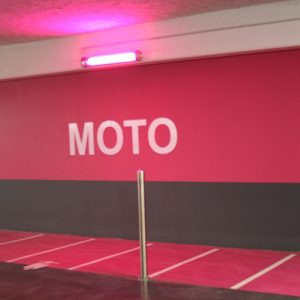
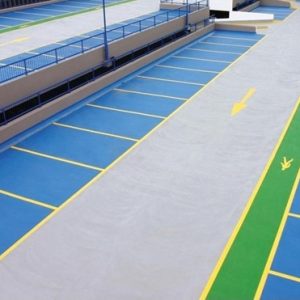
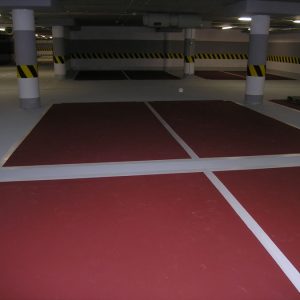
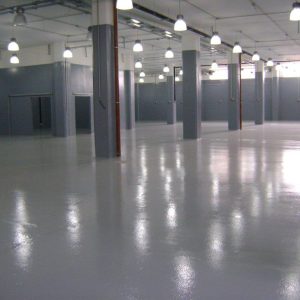

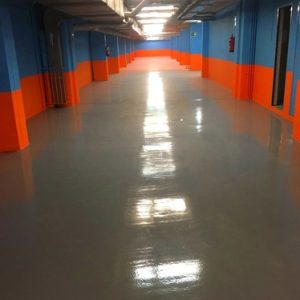
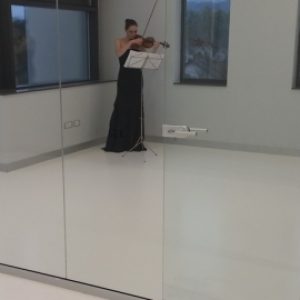
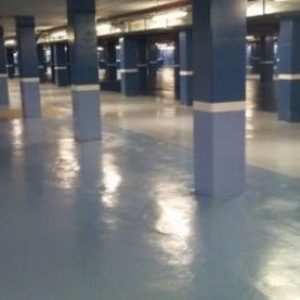
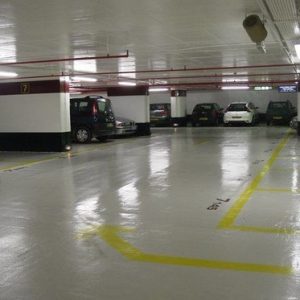
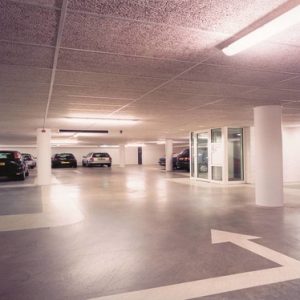
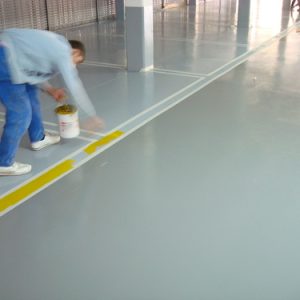
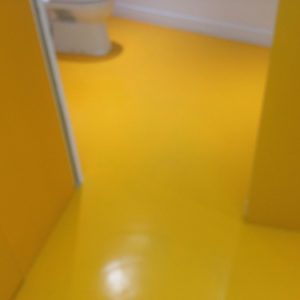

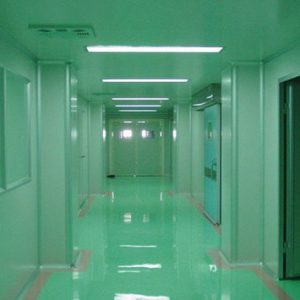
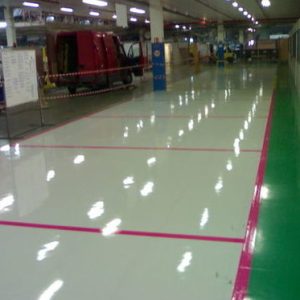
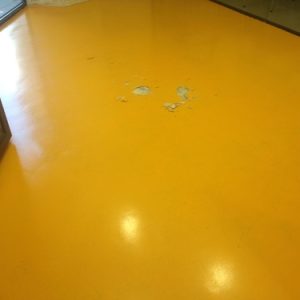
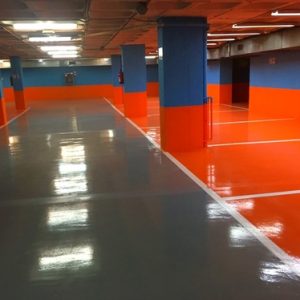
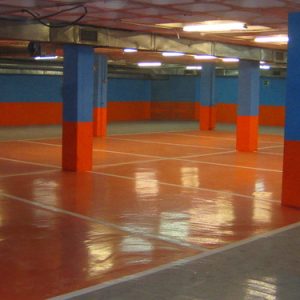
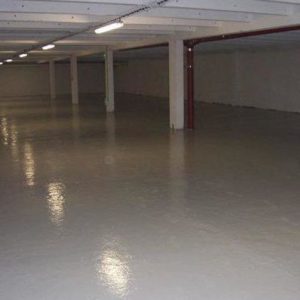
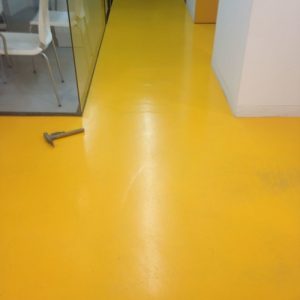
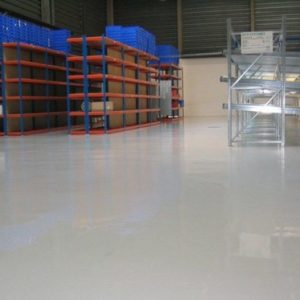
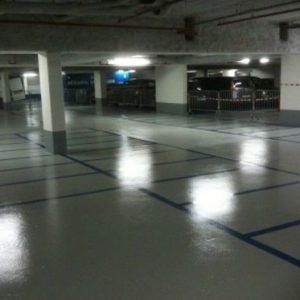
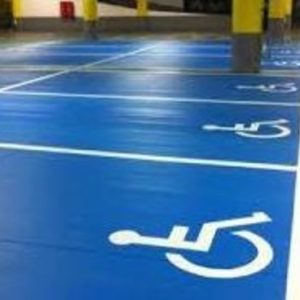
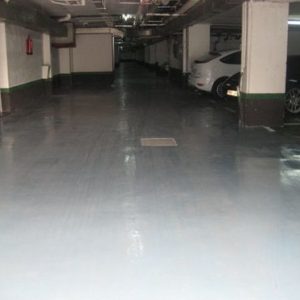
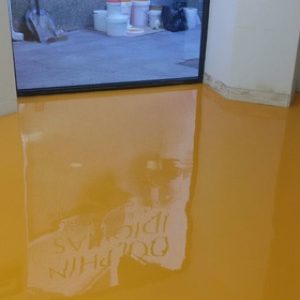
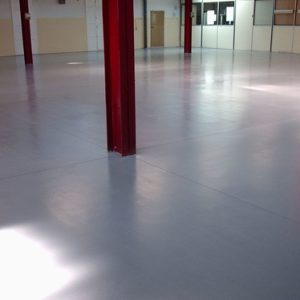
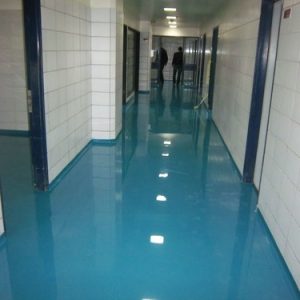
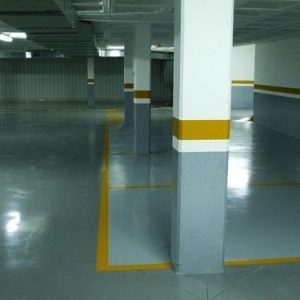
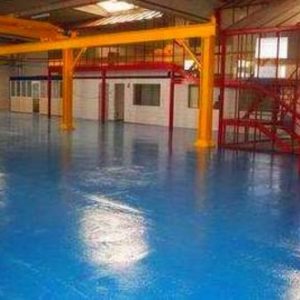

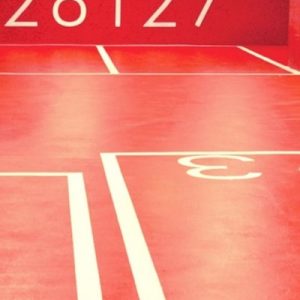
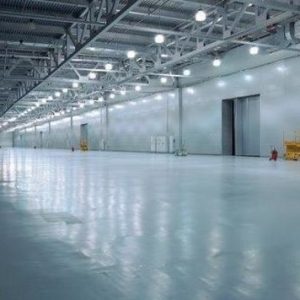
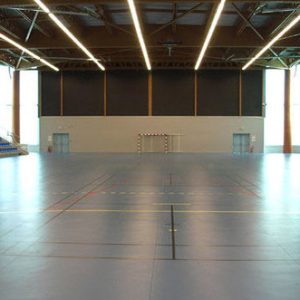
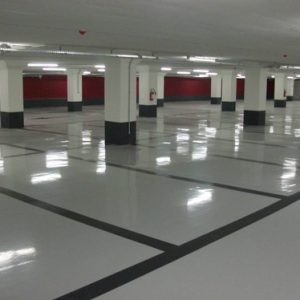
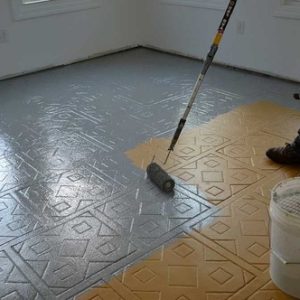
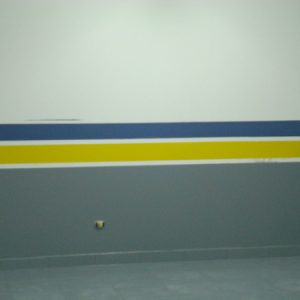
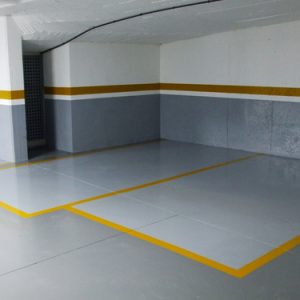
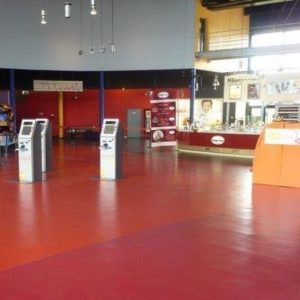
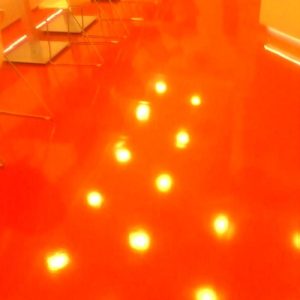
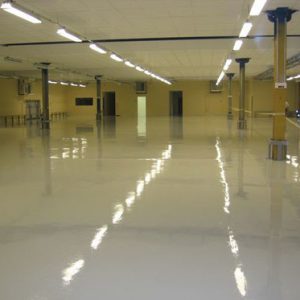
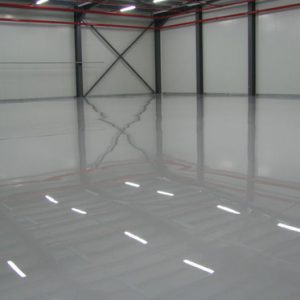
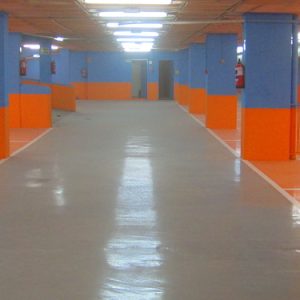
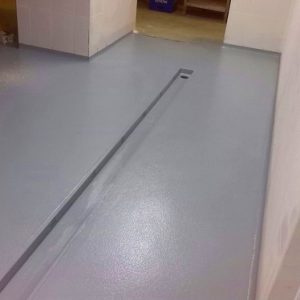
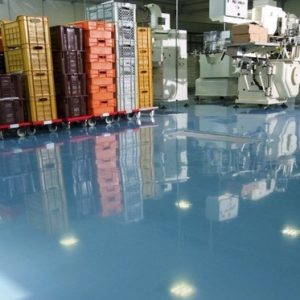
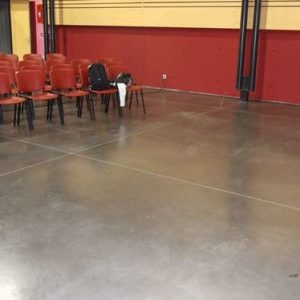
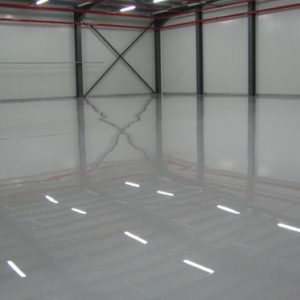
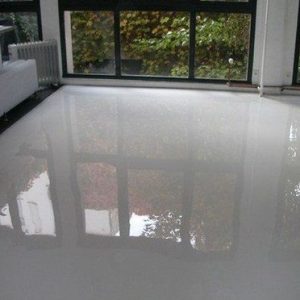
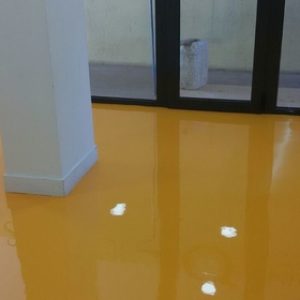
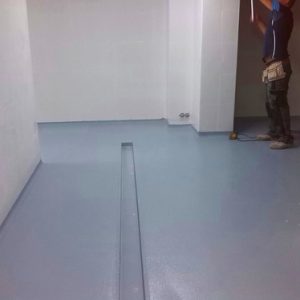
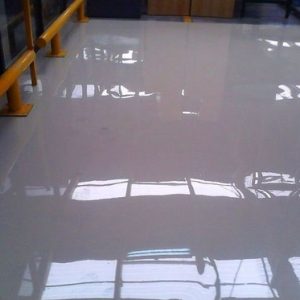
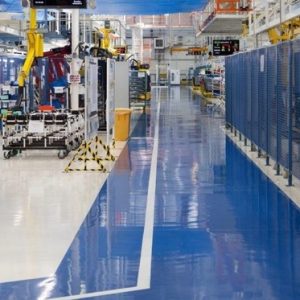
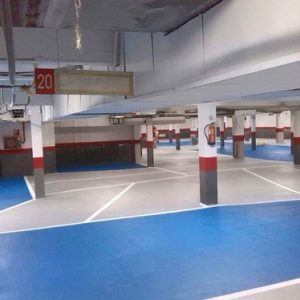
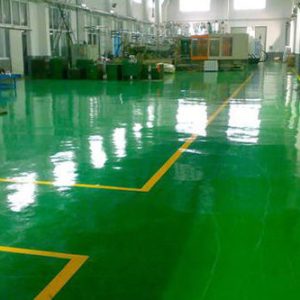
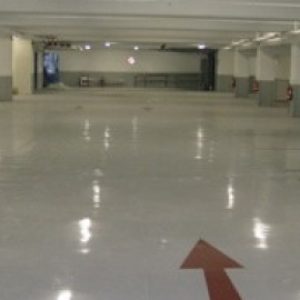

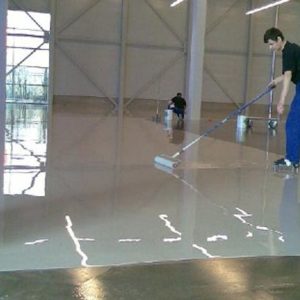
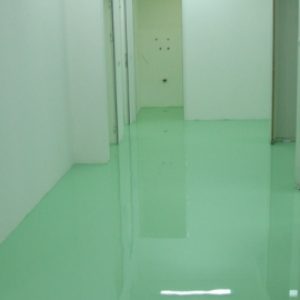
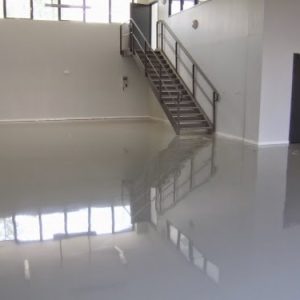
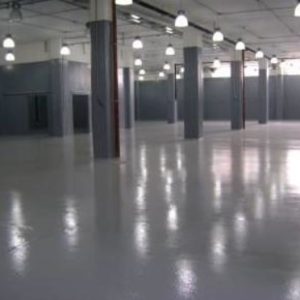
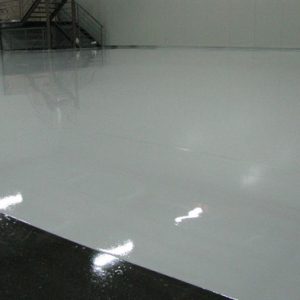
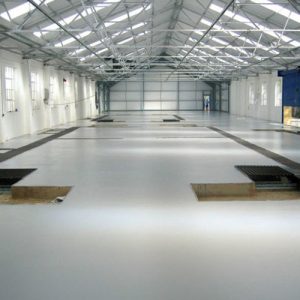
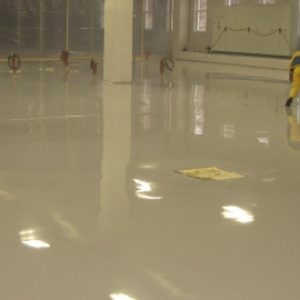
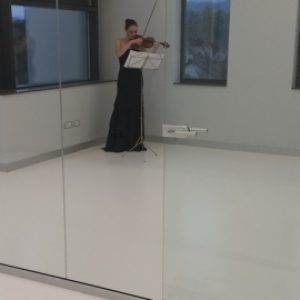
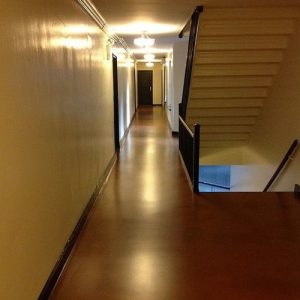
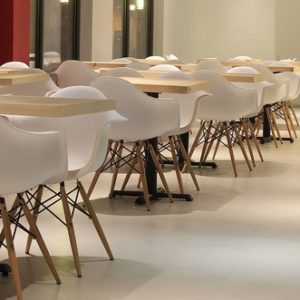
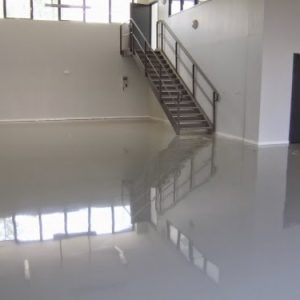
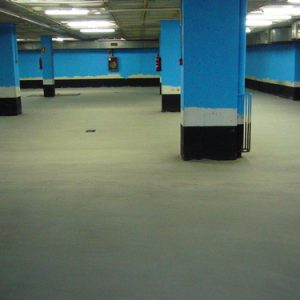
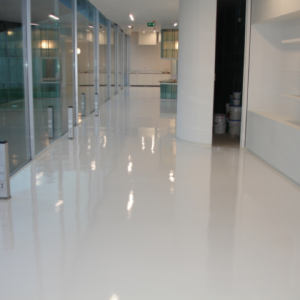
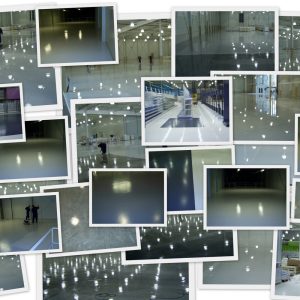
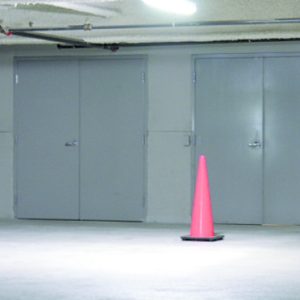
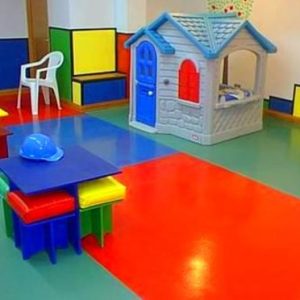
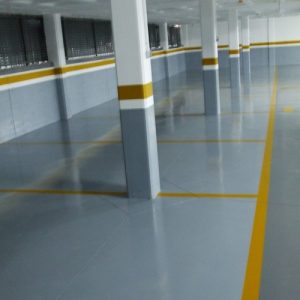
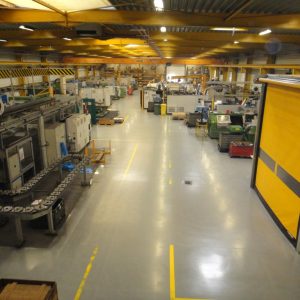
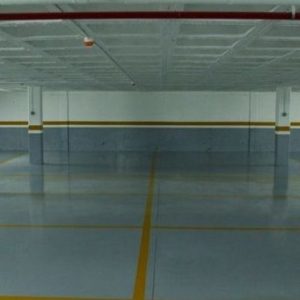
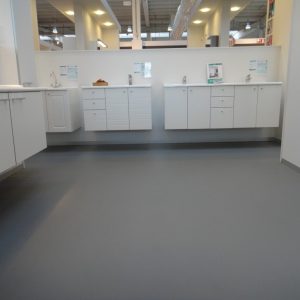
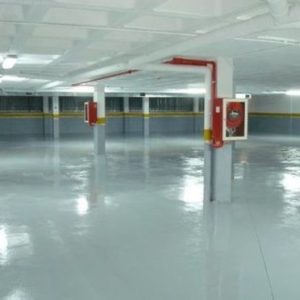
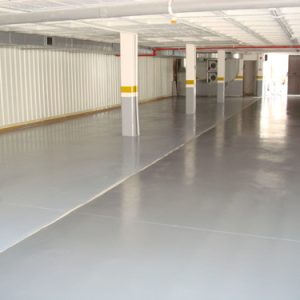
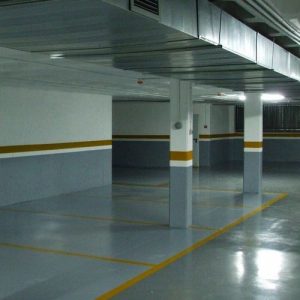
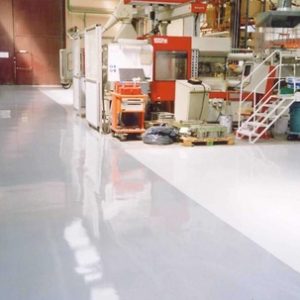
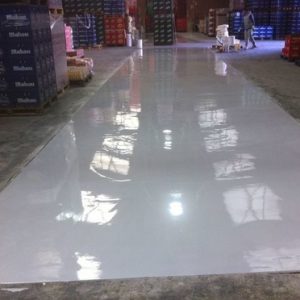
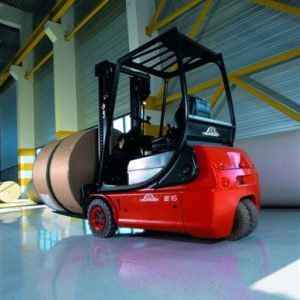
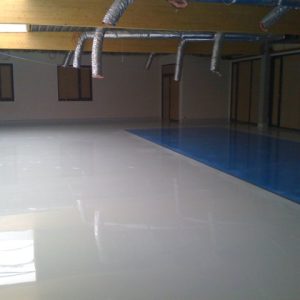
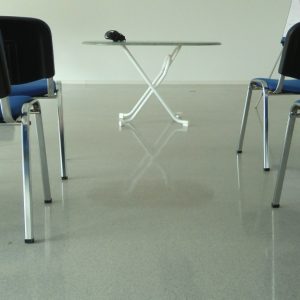
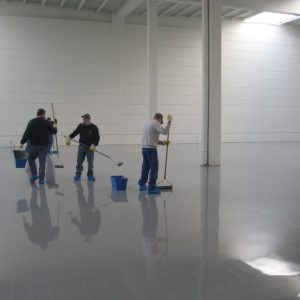
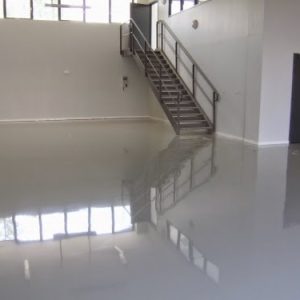
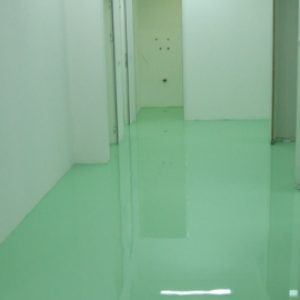
¿Qué es y para qué sirve una resina epoxi?
Pavimentos de resina epoxi: la mejor elección
- Para superficies irregulares: en determinadas zonas es muy difícil obtener una óptima preparación de la superficie. Algunos recubrimientos de pintura epoxi modificado son considerados «epoxis apropiados para superficies irregularmente preparadas» y se pueden aplicar hasta en superficies húmedas.
- Resistente a la abrasión: los pavimentos decorativos con pintura epoxi son más resistentes a la abrasión que las pinturas de otras tecnologías (como los acrílicos, el clorocaucho, los alquídicos, etc.).
- Propiedades: la pintura epoxi es completamente atóxica, sin disolvente y sin olor en interiores. No presenta juntas y tiene un acabado continuo sin contaminación por bacterias o microorganismos. Evita la corrosión del hierro, impermeabiliza el hormigón, evitando su destrucción y resiste a los ácidos carbónicos y sulfurosos. Resistente hasta temperaturas de +70 ºC.
- Proceso estándar para pavimento multicapa: preparación del soporte, limpieza mecanizada (granallado, fresado, lijado y limpieza química), reparación de juntas y fisuras, reparación de desperfectos, aplicación de primera y segunda capa de resina, lijado superficial, aplicación de tercera y cuarta capa de resina.
Pavimentos de resina epoxi continuos sin juntas para viviendas y locales comerciales e industriales
Los pavimentos de resina epoxi se dividen en 3 grandes grupos: según su cantidad de producto de resina sintética acrílica epoxi poliuretánica y su técnica de aplicación, podemos definir como tratamiento la resina epoxi que se aplica en capas delgadas a modo de pintura. Se utiliza como capas finales del sistema de recubrimiento epoxi, para el mantenimiento de suelos epoxi, pero este sistema no puede ser aplicado para la industria, al ser de muy bajo espesor, porque en este tipo de industrias las solicitaciones de resistencia y durabilidad son extremas. Para una información más detallada del proceso de pavimentos decorativos y de resina epoxi, pida información a nuestro personal, que le guiará a lo largo del mismo. En función del pavimento y las necesidades del cliente, se puede modificar el sistema siempre bajo la supervisión de nuestro departamento técnico.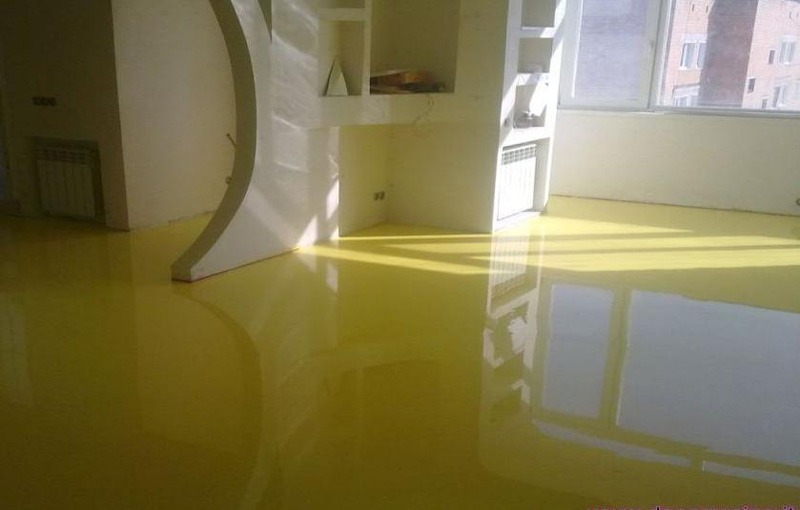
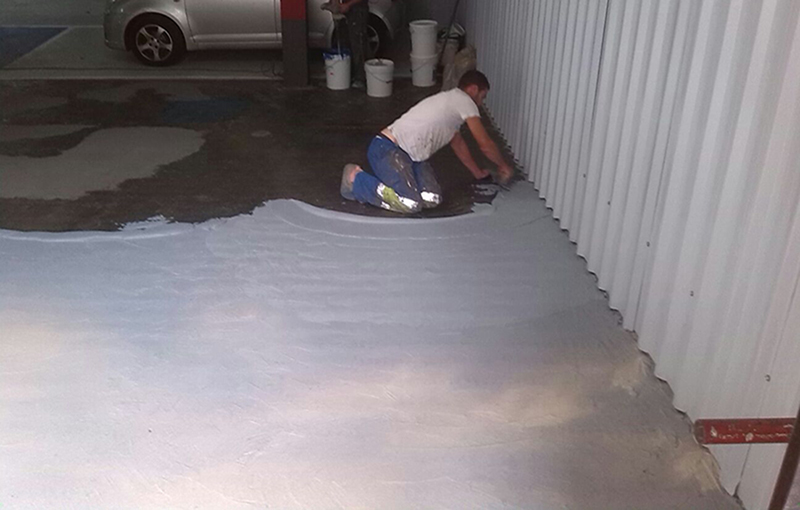
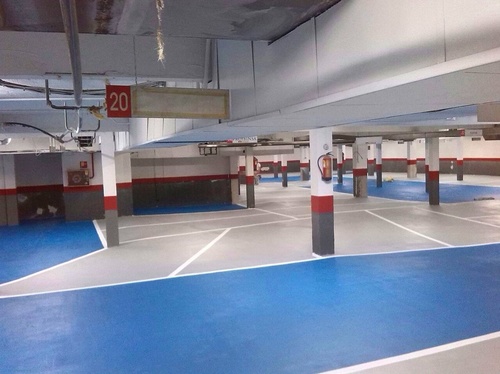
Guía y especificaciones para la aplicación de suelos de resina sintética
A continuación, en secciones separadas, os ofrecemos una guía que da recomendaciones para la clasificación, para el diseño, para la preparación del sustrato, para la aplicación y para la inspección y pruebas del suelo de resina sintética. Su ámbito de aplicación incluye todos los pavimentos a base de ligantes de resinas sintéticas líquidas, en el que el curado tiene lugar por reacción química de los componentes de resina, aplicado a una losa de hormigón acabado directa o solado o a un piso de hormigón existente. La terminología «resina» se deriva de la resina epoxi en la que se basaron los primeros pavimentos de resina. Muchos tipos diferentes de productos químicos se utilizan ahora para la fabricación de pavimentos de resina, pero la característica común es que una polimerización o «reacción de curado» se lleva a cabo in situ para producir el acabado de resina sintética final, los suelos de resina sintética están disponibles en una amplia gama de espesores. El suelo resultante puede proporcionar una superficie con un rendimiento mucho mayor en comparación con la base de hormigón sobre la que se aplica. Las principales ventajas de los pavimentos de resina sintética se pueden resumir como sigue:- Una fuerte unión permanente a la base de hormigón.
- Excelente resistencia a un amplio espectro de productos químicos agresivos.
- Impermeable a los líquidos.
- Aumento de la dureza, durabilidad, resistencia, y la resistencia al impacto o la abrasión.
- Superficies higiénicas y de fácil limpieza.
- Mayor resistencia a la fisuración.
- Bajo espesor aplicado.
- Instalación rápida y de curado con una interrupción mínima para las operaciones normales.
- Este documento es la base para el nuevo Código Estándar de Prácticas para suelos sintéticos BS 8204-6 resina Pavimentos.
Suelos de resina sintética
Para todos los productos de suelos de resina sintética la reacción de fraguado, por el cual los componentes inicialmente líquidos se convierten en un polímero duro fuerte, comienza solo cuando la resina base y el endurecedor reactivo se mezclan íntimamente. Para obtener los resultados óptimos estos componentes deben ser mezclados en las proporciones precisas necesarias para la reacción química que se produzca y el mezclado debe ser a fondo para asegurar que el producto final es homogéneo y uniforme en las propiedades.Tipos de resinas sintéticas
Una variedad de diferentes tipos de sistemas de resinas sintéticas están disponibles que puede formar el aglutinante de un sistema de suelo. Estos incluyen típicamente epoxi, poliuretano y resinas de metacrilato. Diferentes tipos de resina dan diferentes combinaciones de características de aplicación y el rendimiento en servicio y las consideraciones que afectan a la selección de un tipo particular están descritas en la sección de diseño.Clasificación de tipos de suelo de resina sintética
Los suelos de resina sintética se pueden dividir en diferentes tipos que varían en espesor y acabado de la superficie:- Sellado. Aplicado en dos o más capas. Generalmente disolvente o transmitidas por el agua. LD hasta 150 micras.
- Pavimento de suelo aplicado en dos o más capas. Generalmente libre de solventes. LD / MD 150 micras a 300 micras.
- Pavimento de suelo de alto espesor aplicado en dos o más capas. Generalmente libre de solventes. De 300 micras a 1000 micras.
- Suelos multicapa. Agregados a los sistemas de vertido sobre la base de múltiples capas de recubrimientos de suelos o pavimentos a menudo descrito como sistemas de «sándwich». MD / HD > 2 mm.
- Autonivelantes. «Auto-suavizado» o pisos «autonivelantes» y que tienen una superficie lisa. MD / HD 2 mm a 3 mm.
- Morteros de resina. Generalmente incorporan una capa de sellado de superficie para minimizar la porosidad. MD / HD > 4 mm.
- Tráfico pesado. Para áreas pesadas suelos de fluido que tiene una superficie lisa. HD / VHD 4 mm a 6 mm.
- Suelos de resina de alta resistencia. Sistemas de relleno con agregado impermeables a lo largo de su espesor. VHD > 6 mm.
Sostenibilidad
Los suelos de resina no presentan un peligro medioambiental. La Hoja de Datos de Seguridad define los peligros y los requisitos para minimizarlos. Todos los usuarios de materiales peligrosos deben tener los requisitos de la Hoja de Seguridad y producir una evaluación COSHH (Control de Sustancias Peligrosas para la Salud). Esto les informa de los peligros y detalla lo que necesitan hacer para protegerse a sí mismos.Información
Consultas e intercambio de información entre todas las partes interesadas con las operaciones de construcción deben ser dispuestos de manera que cada uno tiene pleno conocimiento de las particularidades de la obra suelo y ser capaz de cooperar en la producción de las condiciones requeridas para completar un trabajo satisfactorio. Algunos de los temas que figuran a continuación (información que se debe proporcionar al contratista de los pisos, que este debe aportar y el horario) pueden necesitar precauciones adicionales o procedimientos y la responsabilidad de estos deben determinarse de antemano de la obra.Selección de los suelos donde se aplicará
Es esencial que, en las etapas de diseño y construcción, debe haber plena consulta con el fabricante del producto del suelo y/o el contratista de pisos especialista para asegurar que el producto que se ha seleccionado es totalmente adecuado para las condiciones tanto durante la aplicación y en su posterior servicio.- Uso del suelo de resina sintética incluyendo el tipo, el alcance y la frecuencia de tráfico previsto;
- Tipo de carga, estático o dinámico, y la gravedad de impacto;
- Detalles de todos los productos químicos, incluidos los utilizados para la limpieza o esterilización, que podría entrar en contacto con el suelo, y el alcance, la frecuencia y la temperatura de vertido;
- Las temperaturas que requiere el suelo para soportar en servicio normal o como parte de las operaciones de limpieza y si la exposición es por el calor radiante o conductor o por contacto directo;
- Color, la uniformidad y la retención, la estética y efectos decorativos n que el suelo va a estar expuesto a la luz solar directa o luz ultra-violeta;
- El cumplimiento de los requisitos de higiene o de la industria alimentaria;
- Requisitos especiales, tales como la resistencia al deslizamiento o características controladas estáticas;
- Vida esperada del suelo;
- Espesor de suelo para ser instalado;
- Tiempo disponible para la aplicación y el curado del suelo;
- La edad, la especificación si se conoce y la naturaleza de la base, incluyendo información sobre cualquier uso anterior de la planta, que podría afectar a la adhesión, y cualquier tratamiento preparatorio necesario.
Información que debe proporcionarse a la contratista de pisos
Toda la información relevante debe ser proporcionada a su debido tiempo a los responsables de la instalación del suelo y de otros cuyo trabajo podría verse afectado, incluyendo cualquiera de los siguientes:- Descripción, situación y dirección del sitio y medios de acceso;
- Ubicación y área de suelo que se instalarán;
- Nivel del piso terminado.
- Clase de regularidad de la superficie del piso terminado;
- Tipo de impermeabilización y el aislamiento si está presente;
- Tipo y el espesor de cualquier capa de regularización que se propusieron, y si cualquier compuesto de curado que se va a aplicar;
- Tipo de acabado de la base de hormigón o pavimento;
- Tratamiento de canales;
- Tratamiento de zócalos y bordillos;
- Tratamiento de los cruces con pavimentos adyacentes y los umbrales;
- Requisitos especiales relacionados con la calefacción por suelo radiante;
- Momento de la introducción de la calefacción en el edificio;
- Fecha para la finalización de la base o capa de hormigón para recibir el suelo;
- Las fechas de inicio y finalización de varias secciones de la planta;
- Detalles de cualquier prueba de conformidad requerida;
- Las posibles restricciones a las horas de trabajo;
- Cualquier limitación en la instalación debido a la producción u otras actividades.
Información que debe ser proporcionada por el contratista de pisos
El contratista de pisos debe proporcionar a su debido tiempo a los responsables de la construcción, los detalles de las condiciones necesarias para la instalación del piso, incluyendo:- La extensión de las áreas resistentes a la intemperie que debe proporcionarse para el almacenamiento de las materias primas y la mezcla del producto del suelo y si cualquier control de la temperatura es necesario;
- Requisitos de temperatura ambiente en la zona donde el suelo se ha de instalar;
- Requisitos de energía y de iluminación para facilitar la operación de colocación;
- Protección para aislar el área de trabajo de las instalaciones adyacentes;
- Intervalos de tiempo mínimo después de que el suelo se instala antes de permitir el tráfico peatonal, el tráfico vehicular y agua o la exposición química.
- Protección necesaria para el suelo entre la instalación y entrega final.
Horario
- Curado y el secado del hormigón base, solado de hormigón fino, y / o cementoso capa de regularización modificado con polímero, cuando sea aplicable;
- El tiempo entre el comienzo y la finalización de los trabajos;
- Período de curado y protección del suelo de completado del daño causado por otros oficios, incluyendo restricción de acceso.
Diseño
Parámetros de selección
Entre los factores que influyen en la selección de un sistema de suelo se incluyen:- Tipo y grado de tráfico
- Las temperaturas a las que estará expuesto suelos
- La naturaleza y duración de cualquier contacto químico con el piso
- Condiciones de servicio húmedas o secas
- Requisitos de resistencia al deslizamiento
- Facilidad de limpieza (incluidos los requisitos de higiene)
- Contenido de humedad del sustrato
- Tiempo disponible para la aplicación y el curado del pavimento
- Alteraciones en el lugar que prevalece en el momento de la instalación
- Costo
Durabilidad
En términos muy generales la vida de servicio será proporcional al espesor aplicado de los pisos de resina sintética. Sin embargo, muchos factores operacionales afectan directamente el rendimiento incluyendo la gravedad del tráfico (tipo de rueda y carga), la frecuencia y la eficiencia de la limpieza, el abuso y la manipulación mecánica de impacto, etc. En la mayoría de las instalaciones industriales habrá una variedad de situaciones para cada uno de que un tipo diferente de suelo de resina sintética será más apropiado. Por el contrario, habrá áreas en las que algunos tipos son totalmente inapropiadas.Homogeneidad de la superficie y la resistencia al deslizamiento
El piso terminado debe dejarse curar de acuerdo con las instrucciones del fabricante. Estos generalmente requieren de 1 a 3 días a 15 – 20 °C antes de permitir un uso significativo por el tráfico y 3 a 7 días a 15 – 20 ° C antes de la limpieza en húmedo, lo que permite el contacto con productos químicos, o el tráfico pesado. Algunos suelos de resina, en particular las basadas en resinas de metacrilato de metilo (MMA) pueden curar mucho más rápido para lograr un desempeño completo en cuestión de horas. Esto los hace adecuados para proyectos de ejecución rápida o aplicaciones a temperaturas de congelación, por ejemplo en cámaras frigoríficas. Como regla general, el suelo de una superficie más suave y menos poroso, es más fácil de mantener limpio. Sin embargo, superficies de textura gruesa son más difíciles de limpiar, por lo que tanto la resistencia al deslizamiento y facilidad de limpieza son importantes, el suelo debe ser seleccionado con la textura suficiente para adaptarse a las condiciones de trabajo y las normas específicas de higiene, y un programa de limpieza eficaz frecuente se debe establecer en su lugar. Aparte de la selección de los suelos, el uso en zonas húmedas especialmente de calzado especial con suelas antideslizantes puede ser beneficiosa al permitir un acabado más suave del suelo que ha de adoptarse.Resistencia química
Los suelos de resina sintética bien formulados y aplicados correctamente han demostrado ser un método eficaz de proteger los sustratos de hormigón sensibles al ataque de derrames agresivos. El fabricante o contratista para decidir qué producto recomiendan para una situación particular requerirá información sobre:- Constituyentes químicos y la concentración de la probabilidad de derrame.
- Temperatura del derrame.
- Cantidad y frecuencia de la derrame.
- Presencia de agua y procedimientos para la emergencia de lavado.
- Procedimientos de limpieza habituales.
- Caídas, drenaje y sumideros.
Color y resistencia a los rayos UV
Los suelos de resina sintética se selecciona generalmente para su uso debido a los requisitos específicos de rendimiento que otros suelos no pueden alcanzar. Como consecuencia, la gama de colores disponibles ha sido tradicionalmente limitada por la disponibilidad de los pigmentos con el nivel requerido de resistencia química. Sin embargo, existe una tendencia creciente a colores más claros y brillantes que se requieren con el fin de mejorar el entorno de trabajo general. El producto de suelo se debe utilizar en estricta rotación lote para evitar las variaciones menores inevitables en sombra resultado de la fabricación por lotes. Además, ligeras variaciones en el color pueden resultar de variaciones en las condiciones ambientales y técnicas de aplicación. Se debe tener cuidado en la selección de los suelos en las zonas donde la superficie esté expuesta a la luz solar o a la radiación ultravioleta. Algunos pigmentos y aglutinantes de resina sintética, siendo de naturaleza orgánica se decolora en la exposición prolongada. Si la apariencia estética es un requisito importante entonces el sistema de piso se debe elegir en consecuencia.Estática controlada
Es importante a seleccionar el sistema que mejor se adapte a los requisitos para el entorno de trabajo. El color debe ser discutido con el fabricante de suelos, ya que puede haber ciertas limitaciones de color en suelos anti-estáticos debido al efecto de oscurecimiento de carbono.Resistencia a la temperatura
La mayoría de los pavimentos de resina sintética tienen temperaturas relativamente bajas de distorsión por calor (HDT), generalmente entre 50 y 100 °C, mucho más bajas que las baldosas cerámicas o suelos de hormigón. En la práctica ciertos suelos de resina sintética han demostrado ser capaces de resistir temperaturas considerablemente más altas que su HDT través de la atención a la formulación, aplicación y diseño de planta, los suelos de resina sintética por lo general no deben ser expuesto directamente a temperaturas superiores a 100 °C. La resistencia de un suelo de resina sintética dependerá de una serie de factores:- Naturaleza y tipo de fuente de calor.
- Debido a la baja capacidad térmica del aire y de los relativamente lentos cambios en la temperatura causados por el calor de la convección y el radiante, el calor seco es normalmente un problema sólo en condiciones extremas, por ejemplo cerca de horno en las puertas, especial cuidado debe tomarse en el diseño del pavimento donde las variaciones extremas de temperatura es probable, como en cámaras frigoríficas y las áreas alrededor de los hornos. El movimiento de estas áreas en relación con el suelo circundante debe considerarse cuidadosamente y se instalan juntas apropiadas.
- Las caídas mínimas para desagües de 1,5%.
Las condiciones de curado
El piso terminado debe dejarse curar de acuerdo con las instrucciones del fabricante. Estos generalmente requieren de 1 a 3 días a 15 – 20 °C antes de permitir un uso significativo por el tráfico y 3 a 7 días a 15 – 20 °C antes de la limpieza en húmedo, lo que permite el contacto con productos químicos, o el tráfico pesado. Algunos suelos de resina, en particular las basadas en resinas de metacrilato de metilo (MMA) pueden curar mucho más rápido para lograr un desempeño completo en cuestión de horas. Esto los hace adecuados para proyectos de ejecución rápida o aplicaciones a temperaturas de congelación, por ejemplo en cámaras frigoríficas. Un curado adecuado siempre se debe permitir antes de la prueba húmeda del suelo para el drenaje o encharcamiento. A temperaturas debajo de 10 °C, los tiempos de curado se incrementará sustancialmente menos que se utilice algún tipo de calentamiento externo.Membranas a prueba de humedad
En las nuevas construcciones, para las bases de hormigón en contacto con el suelo, una membrana a prueba de humedad debería haber sido incorporado en el diseño de la losa, de conformidad con los requisitos de CTE.Regularidad de la superficie
Debido a su método de aplicación, los pavimentos de resina sintética instalados inevitablemente deben seguir el perfil del sustrato subyacente. Por lo tanto, las normas acordadas para la llanura, la regularidad y la conformidad del piso al actualizar los pisos existentes, los medios para obtener los niveles requeridos y planitud deben ser acordadas de antemano.Superficie regularidad
La clase o categoría de regularidad de la superficie requerida para una superficie de suelo dependerán del uso del suelo.Caídas o pendientes
Un suelo de resina sintética en particular con una textura de superficie rugosa no drena el agua o efluente líquido satisfactoriamente a menos que se introducen caídas suficientes.Juntas
El espaciado de las juntas de movimiento debe ser determinada por el diseño del subsuelo. Todas las juntas de movimiento existentes en el subsuelo deben ser realizadas a través del suelo de resina sintética. En todos los casos la necesidad de juntas de movimiento y su tipo y posicionamiento debe ser acordado en la etapa de diseño entre todas las partes interesadas.Canales
Los canales se incorporan normalmente en sistemas de piso para transportar líquidos, como derrames y agua de lavado a los desagües adecuados. Las pendientes o caídas adecuadas deben ser instaladas. Un detalle de uso común es un canal de acero inoxidable preformada. Estos están sujetos a movimiento diferencial y deben tener una junta flexible entre el suelo y el canal. En ambientes agresivos, un enfoque alternativo es alinear los canales de drenaje con el piso relleno con el fin de mantener una superficie monolítica, evitando así juntas en zonas vulnerables.Sistemas pintura Epoxi-Poliuretano
Los pavimentos de hormigón están expuestos a constantes agresiones mecánicas y químicas. Todos nuestros revestimientos de pavimentación en continuo proporcionan alta protección, buen acabado y gran facilidad de mantenimiento y limpieza, aspectos vitales para garantizar el desempeño y la durabilidad. También es posible la ejecución con diferentes acabados antideslizantes.Propiedades de los sistemas de pintura epoxi-poliuretano:
- Excelente adherencia al hormigón, mortero y piedra.
- Buena resistencia mecánica, a la abrasión y al impacto.
- Buena resistencia química.
- Impermeable al agua.
- Acabado decorativo, gran variedad de colores con acabado brillante o satinado. Liso o rugoso.
Descargas
- Presentación – Parking Pavipor
- ¿Qué es una imprimación epoxi? Ver o descargar ficha técnica
- ¿Qué es una pintura epoxi? Ver o descargar ficha técnica
- ¿Qué granulometría de sílice o cargas micronizadas se utilizan en los sistemas epoxídicos? Ver o descargar ficha técnica
- ¿Cómo se construye un pavimento epoxi multicapa para las industrias? Ver ficha técnica